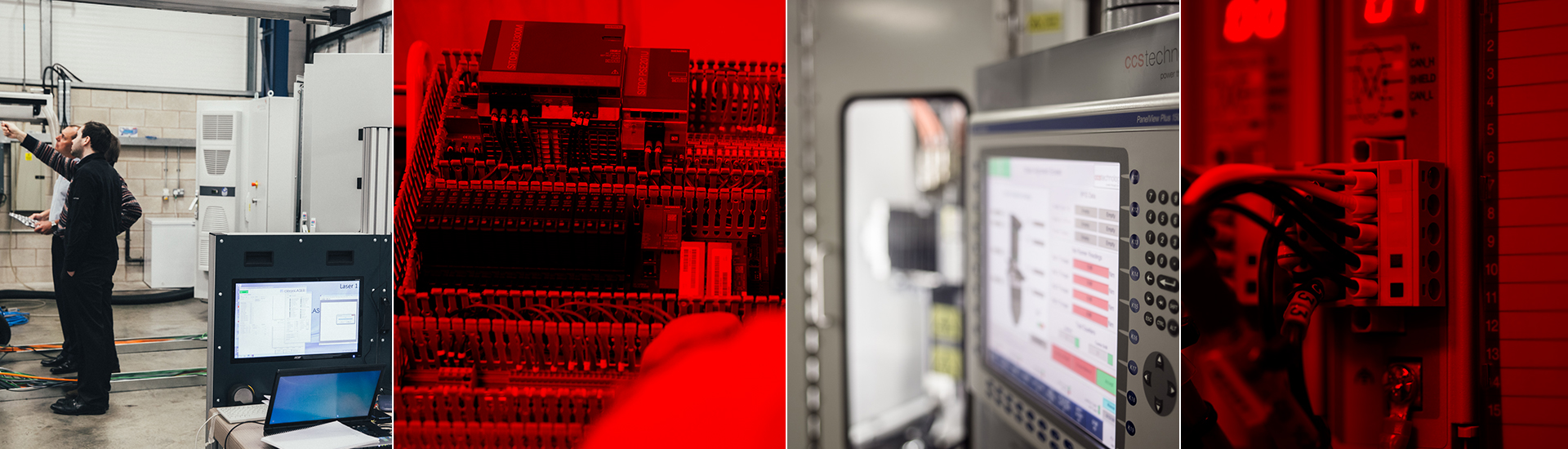
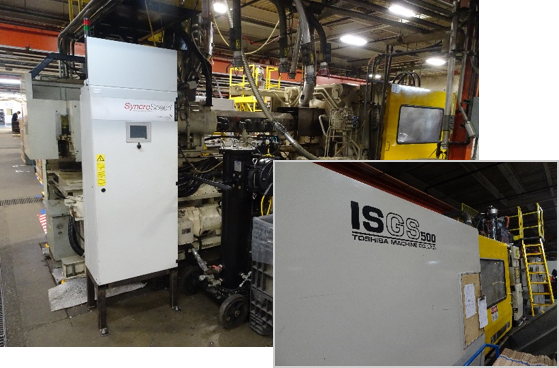
SyncroSpeed installed on a 500t Toshiba, driving a single 75 HP motor.
Injection moulding of plastic parts is a prime manufacturing process that is behind the availability of goods and components in just about every conceivable market segment.
You get up and shower, with water supplied and drained through installed plastic pipes and fittings, a quick check on your mobile phone or TV while grabbing some breakfast out of the fridge gets you close and personal with many objects carefully engineered and constructed with plastic parts. Then the drive to work, with many exterior and interior components finishing off the pleasing function and form of your car. Your workstation surrounds you with all sorts of gadgets and technology, perhaps most important being the one where you place your bum … the office chair with its ergonomic support and attractive lines all made feasible with injection moulded parts. At last back home and playtime with the kids … it could Lego, the plastic brick since the 1950’s and made with a popular engineering thermoplastic called ABS. Later a meal for two, maybe some cooking with measuring jugs, spoons, chopping boards all in fave accent colours, easy to use, easy to clean. Finally to bed and off with the light … the switch could well be plastic too, probably a thermoset!
All these durable components are produced by injection moulding machines which consume electricity hour-by-hour, day-by-day, and they are expected to remain in effective production for at least 20 to 30 years, often longer. That’s a lot of energy and a lot of associated CO2, which is where SyncroSpeed steps in centre stage. With our retrofit systems, SyncroSpeed eliminates 20% – 50% of the moulding machines energy consumption, and across the globe that adds up to a whole less cost and less CO2 emissions for the producers of plastic products. These retrofits are good for business and great for the planet.
SyncroSpeed’s reach is global – systems are deployed by moulders from Korea to California, and even NZ in between! Recent projects are for a European manufacture of components for the Renault Megane, a branded manufacturer of brushes, brooms and other household goods in Portugal, and a Toronto based plant producing components used in house construction.Our goal is to improve the efficiency and eliminate tonnes and tonnes of CO2 throughout the injection moulding world.