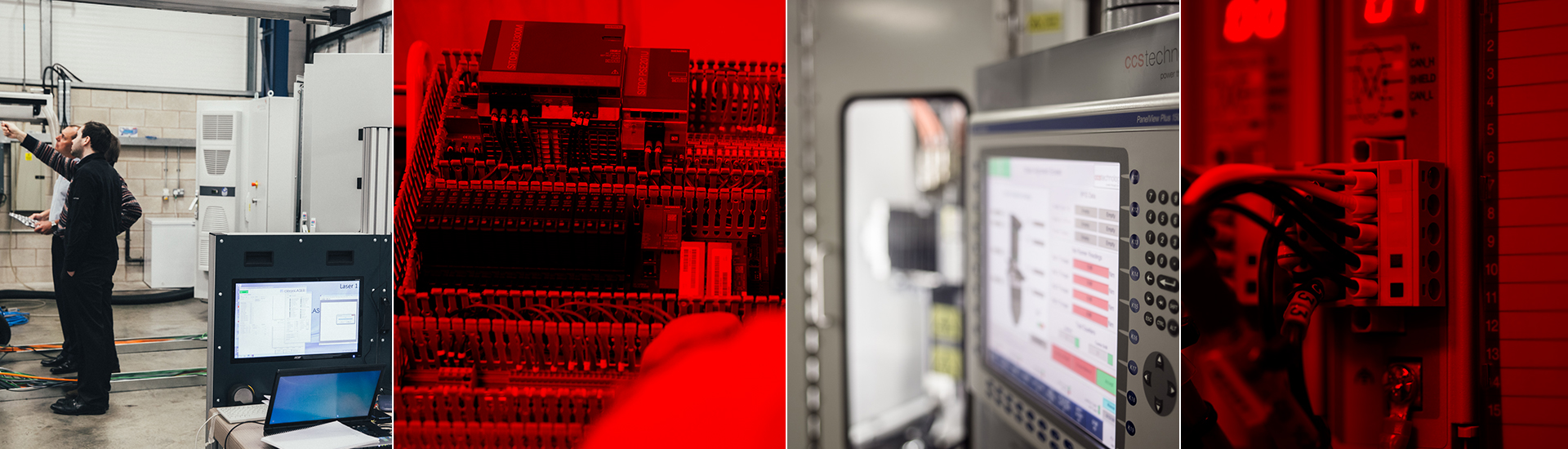
Cricket isn’t the only game in town, as the SyncroSpeed crew admirably demonstrated down under in Auckland, New Zealand. The energy-saving team put in a great performance, delivering considerably more cost savings for the Kiwi injection moulder than was first estimated. The visitors notched up an annual saving of over NZ$60,000 across three IMMs, leaving the customer not only impressed with the technology, but delighted with the results.
fast pace
When the pressure is on to get a great result, SyncroSpeed offers matchless capability in determining where and how to reduce motor power throughout the moulding cycle; the retrofit system assesses optimum motor speed around 50 times each second to build the maximum possible energy saving each cycle without affecting cycle time, the injection profile, or part quality.
e the results with SyncroSpeed systems recently installed on three IMMs in New Zealand. The major benefit was to reduce motor power consumption by 66 kW and save NZ$60,000 in energy costs each year. The inset is a picture of the SyncroSpeed touch screen HMI for the 2-motor IMM.
winning score
Ranging 360t – 550t, these machines are powered by electric pump sets up to 55 kW and run night and day, 5 days each week. Following an initial assessment, the target was to reduce the total operating power consumption of the motors on three injection moulding machines by at least 29 kW. Installation of the SyncroSpeed systems took 4 days to complete, followed by 2 days of calibrating and refining the SyncroSpeed control software, during which the likely savings looked very promising. At the close of play the final result was an impressive 66 kW reduction, a 51% saving, in all cutting the moulding energy costs by around NZ$ 60,000 each year, plus another NZ$ 3,200 in reduced operating costs of the cooling towers.
practice & consistency
The performance of SyncroSpeed is founded on hundreds of installations on all popular brands of injection moulding machine, with highly developed software capable of finding and delivering every possible reduction in motor energy consumption. It’s a world-class combination of advanced technology and deep-rooted know-how, ready to match any challenge the injection moulding world has to offer.
The SyncroSpeed system comprises an inverter and industrial plc assembled in a steel enclosure with status and performance data available via a touch screen HMI
key data
clamp
pumps
plasticising drive
motor sizes
cycle times
material
shot weight
toggle, 2-platten
fixed volume
hydromotor
37 – 55 kW
35 – 65 s
pvc
200 – 1000 g